SLURS
Under the heading of “slurs” I associate several causes and
cures for part of a printed sheet not seeming clean or crisp—or
seeming “swiped” or smeared.
The sheet is not stripping from the form cleanly after impression, but
follows it or springs against it as the press opens.
Make sure the
packing is flat against the platen and not baggy or sagging, and that the
packing bails are snug. The corners of the tympan can be snipped off to help
draw it tight in the bail.
The sheet itself may be wavy or curled so as not to lie flat against
the packing. Try rolling it or printing the other side. Use gripper bars with
frisket fingers set outside the printing to hold the sheet flat. Sometimes
it is necessary to stretch string or rubber bands between gripper bars on
each side of the printing, or to cut a frisket of plastic or tag to cover
the sheet except where it prints. Tape such friskets in place firmly so
they do not work into the printing accidentally and smash the form. Be sure
that the frisket is not disturbing the register of the sheet.
It is sometimes possible to lock up rules with the form that print
outside the final trim on the sheet. The slur may then be passed to the
rules, leaving the printed area sharp. “Steelpoints”,
slugs with type-high
tacks cast in them, can leave a slight mark on the sheet, but may cure a
worse slur when locked up next to the slurring part of the type.
If coated or very light stock is being run, the ink can be so tacky
that the sheet sticks to the form. Your ink maker can supply you with tack
reducer. A little petroleum jelly or a drop of linseed oil or kerosene
may help. All additions
should be tested as they tend to weaken the skin of the dry ink.
If the ink seems too loose or greasy, try adding “body gum”
or number
eight litho varnish to increase tack. Black inks are usually formulated
with type in mind, but color inks may not print type as well. Let the
press run for a half hour or so to heat and stiffen the ink.
The geometrical relationship between the trucks and rollers is wrong.
The trucks must be very nearly the same diameter as the rollers. If there
is too great a difference, the rollers will be dragged or pushed across
the form, not rolled, applying their ink like a squeegee to the type.
Expandable rubber trucks provide a limited range of adjustment.
The rollers are set too heavy. Roller problems.
The rollers should be truly round and parallel. Check the ink stripe in
several places with a typehigh gauge. A pica-wide stripe is a good general
setting—light forms may require less. The inked type form can be
examined with an eight- or ten-power loupe to determine if the face of
the type is being over or underinked. The ink should be only just showing
on the sides of the type.
More rollers and light ink is better than fewer rollers and heavy ink.
Two old pieces of broad border rule may be locked up to the right and
left of the form to bear the rollers off the ends of the lines of type.
Composition rollers print well but shrink and swell with humidity, and
are seldom truly round. Polyurethane rollers soften over time and finally
dissolve. Rubber rollers are probably the best allround choice and the
cheapest and most easily available. They tend to harden over time, but
this may actually help keep ink off the neck of the type when deep
impression is required.
Clean the trucks and tracks with typewash, and dust them lightly with
powdered rosin to prevent slipping and provide traction. Powdered rosin is
used by printmakers and is available from art supply houses.
On old presses, the fit between the trucks and the roller shafts
may be sloppy. I do not know a good remedy for this.
Evidently, if the trucks are of the same diameter as the rollers,
and the rollers are correctly inking the type, then the tracks must be
nearly type-high above the bed. The tracks on the Heidelberg platen are
easily adjusted (and can even be skewed to suit the form).
Other, old worn presses may require makeshift corrections
by tape or somesuch, or a permanent rebuilding by a machinist.
When the press is not in use, center the rollers in the tracks to
relieve the springs. Do not leave the rollers standing for long on the
ink plate or the form.
The press is worn.
Old presses may have considerable play between their bearing surfaces.
If, under impression, the arms of the press seem loose,
it may be possible to shim their bearings with brass or steel shim stock
from an automotive supplier or a bearings dealer.
Below the delivery table at the front of a Chandler and Price press
are four metal surfaces on each side that wedge together on impression.
Turn the press over by hand to observe their action. These surfaces should
be free of oil or grease. Dust them lightly with a little rosin on the tip
of your finger, with the press off and stopped, of course.
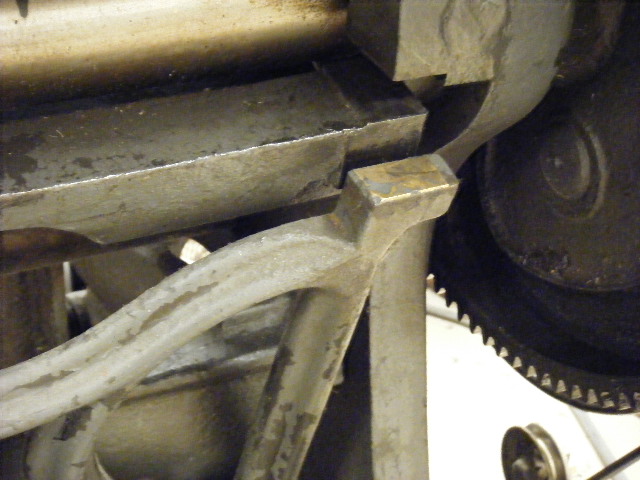
Wrong packing on cylinder presses. Tail whip.
If a cylinder press is very over or underpacked, the circumference of
the cylinder differs so much from the length of the form that it skids
as it rolls.
The tail of stiff stock may whip against the type as it leaves the
cylinder. Steelpoints, or a piece of five-pica furniture locked sideways
along the tail of the form may help.
Home.